Written by Kateryna Kupriienko
A CRE predictive maintenance use case
Imagine a world where you can avoid the inconvenience of a broken elevator in your office building. Predictive maintenance uses data and artificial intelligence to prevent equipment failures, improving operations and reducing costs in commercial buildings. Let's take a closer look at how this works for elevators in a busy office tower, a perfect example of boosting efficiency and keeping tenants happy.
Scenario: the daily pulse of a high-rise workplace
Imagine a bustling 40-story office building teeming with thousands of employees and visitors every day. This high traffic environment heavily relies on its five elevator banks for efficient and seamless movement throughout the building.
Traditionally, elevator maintenance has been a reactive affair, primarily focused on responding to breakdowns or adhering to rigid, time-based maintenance schedules. This approach can lead to:
- unexpected downtime
- inconvenience for tenants
- increased operational costs
For real estate leaders competing in premium office markets, where tenant experience drives property values, this reactive model threatens both building income and asset appreciation.
.webp)
Implementation: giving the building a digital nervous system
To move beyond reactive maintenance, a proactive approach should be implemented. This involves strategically installing sensors throughout the elevator system. These sensors meticulously monitor various critical aspects of elevator operation.
- Vibration patterns in motors and cables: Subtle changes in vibration can indicate impending mechanical issues within the motor or cable systems.
- Door operation (speed and smoothness): Sensors closely monitor the speed and smoothness of door opening and closing, identifying any irregularities that could signal potential problems. Read more about encoders.
- Component temperatures: Precise temperature readings are collected from key components to detect any abnormal overheating, which can be a precursor to more serious malfunctions.
- Usage patterns: By tracking elevator usage patterns, such as peak hours and frequency of stops, building managers gain valuable insights into how the system is being used and can identify areas for potential optimization.
Together, these tools create a comprehensive digital nervous system that transforms each elevator from a simple mechanical transport into an intelligent, self-monitoring system capable of predicting issues before they impact building operations.
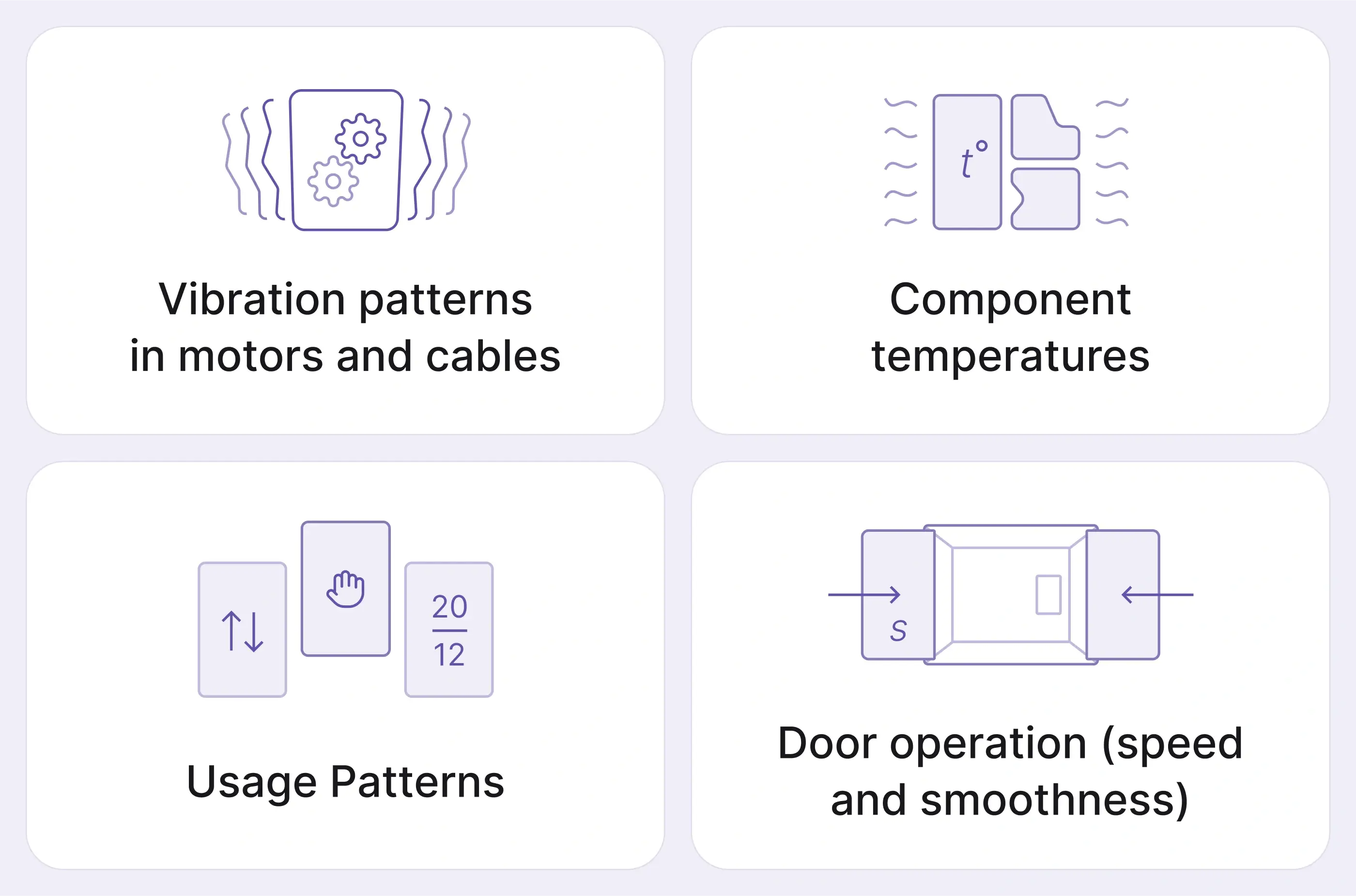
Regular check-ups: orchestrating predictive maintenance
The collected data is continuously streamed and analyzed in real-time. Advanced AI algorithms are employed to identify patterns and anomalies within the data streams. These algorithms can detect subtle deviations from normal operating parameters, signaling potential issues before they escalate into full-blown breakdowns.
This proactive approach empowers building managers with an early warning system, allowing them to schedule maintenance proactively and minimize disruptions to building operations. Find out how Proxet's real estate solutions can unify your data and automate critical workflows.
Example outcome: the power of prevention in action
The system detects subtle changes in an elevator's performance, allowing for proactive, scheduled maintenance. This can reduce elevator downtime by 50%1, translating directly to improved tenant satisfaction and asset value. Beyond the immediate cost savings in maintenance, this dramatic reduction in downtime strengthens tenant retention, preserves property reputation, and ultimately protects asset value that could be eroded by a building's reputation for unreliable vertical transportation.
Benefits: beyond cost savings - a value creation story
Predictive maintenance offers a multitude of advantages for building owners and operators. Let's delve into some of the key benefits:
- Cost Savings: Reactive maintenance, where repairs are made only after breakdowns occur, can be a significant drain on resources. Predictive maintenance flips the script by enabling proactive maintenance. By identifying and addressing potential issues before they snowball into major failures, predictive maintenance can significantly reduce repair costs – by 15-30%2 or more – compared to emergency maintenance. Additionally, by preventing catastrophic equipment failures, predictive maintenance extends the lifespan of elevator components, further reducing long-term operational expenses.
- Improved Tenant Satisfaction: Unexpected elevator breakdowns can disrupt tenant workflows and create frustration. Predictive maintenance ensures a smoother and more reliable elevator experience for tenants. By scheduling maintenance during off-peak hours, when elevator usage is low, there's minimal disruption to daily operations. This proactive approach fosters tenant satisfaction and contributes to a more positive perception of the building's management.
- Operational Efficiency: The data collected by the sensor network in the elevator system provides valuable insights into usage patterns. Building managers can leverage this data to identify peak usage hours and optimize elevator allocation accordingly. This can lead to improved traffic flow and reduced wait times for tenants. Furthermore, by pinpointing areas for optimization, predictive maintenance empowers building managers to allocate resources more effectively, streamlining overall building operations.
How Proxet can help
We have experience designing digital transformations for leading tech-forward companies, and we can help you leapfrog your peers by building intelligent software solutions that put your data to work. Our team has expertise in the most advanced data platforms such as Palantir, Databricks, and Snowflake, and all the major real estate systems like Yardi, MRI Software, and VTS.
Our engineers will focus on using the best technologies to solve your most pressing challenges. For example, we can build a unified data ingestion layer that will check sensor data from your elevators automatically before it goes to the data analytics tools. This means you can trust that the predictions about elevator maintenance needs are based on reliable data.
- According to a McKinsey & Company report titled “Manufacturing: Analytics unleashes productivity and profitability”.
- “JLL Acquires PropTech Building Operations Company Hank” Commercial Observer, https://commercialobserver.com/2022/01/jll-technologies-hank.